01節 一般事項
14.1.1 適用範囲
(a) 金属工事で取り扱う材料・工法は、非常に広範なものであり、一般的な基準は定めにくい。したがって、この章では表面処理、溶接、ろう付けその他について、一般的な標準となる事項を挙げている。
(b) 「標仕」14章では、主として工場で製品化されたものを現場で取り付けることを想定しているので、「標仕」の2節及び3節は、工場製作に対する規定と考えてよい。
(c) 工場地帯、海岸等の金属の腐食の激しい場所にタラップ、丸環等を設ける場合は、人身事故を防ぐために耐食性及び強度の優れたステンレス等を用いることが望ましい。また、丸環については、誤用を避けるため、耐力限度等の使用上の注意事項を明示するとよい。
14.1.2 基本要求品質
(a) 金属工事に使用する材料としては、一般に素材としてのJISが定められているものから、軽量鉄骨下地材のように製品としてのJISが定められているものまで多種多様である。このうち製品としてのJISが定められたものは、一般的な材料と同様に扱えばよい。素材としてのJISが定められた材料を加工して使用する場合にあっては、素材製造工場から製品加工工程を経て.工事現場に搬入されるまでの流れを管理することによって、所定の品質であることを証明できるようにするとよい。
金属工事の表面処理では、素材の規格でなく加工技術の規格としてアルミニウムの表面処理や鋼材の亜鉛めっき等のJISが定められている。これらの指定がされた材料にあっては、表面処理を行った材料が所定の品質であることが要求される。具体的には、表面処理後の材料に対して試験を行い確認することが考えられるが、表面処理工場の実績等を勘案して工場の品質管理記録によって、個々の試験に代えることも考えられる。
なお、表面処理のJISのうち、アルミニウムの陽極酸化皮膜、陽極酸化塗膜複合皮膜及び溶融亜鉛めっきにあっては、「加工技術」に指定されているため、JISの認証加工業者の工場で加工された材料にあっては、改めて材料試験を行う必要はない。
(b) 金属工事の製品は、一般に工場において加工され現場で取り付けられるため、現場で造込みがされる建築工事種目と比べて寸法精度は良いが、設計図書に基づき加工形状や加工寸法を定めるに当たっては、地震時の挙動や日射による熱伸縮の影響等に注意し、下地やその他の材料との取合いを含め、全体の仕上りのバランスを考慮して適切に行わなければならない。
また、金属工事のうち手すりやタラップ等は、使用安全性に直接影響を及ぼすため、堅固に取り付けられている必要がある。製品の取付けに当たっては、事前の取付け方法の検討だけでなく、施工途中の取付け状態の確認等により、完成後の使用安全性を確保できるようにする。
(c) 製品仕上り状態としては、有害な傷や見え掛り部の使用上問題となる傷、汚れ、ねじれ、反り、へこみ等について、あらかじめ限度を定めておき、この限度内に収まっていることと考えればよい。
14.1.3 工 法
(a) 受材の取付け
製品や部材を下地のコンクリート等に金属系アンカーボルト等を用いて留め付ける工法には、「先付け工法」(躯体の施工時にあらかじめアンカーボルト等を設置してコンクリートを打ち込む方法)と「あと施工アンカー工法」(硬化後のコンクリートを穿孔して、この孔にアンカーボルトを固着させる方法)とがある。
(i) 先付け工法
@「標仕」14.1.3(a)では、製品等の受材は、原則として、構造体に損傷を与えるおそれの少ない先付け工法で取り付けることとし、やむを得ない場合にあと施工アンカー工法の類とするとしている。
A 先付け工法に使用するアンカーボルト等には、頭付きアンカーボルト、鉄筋アンカーボルト、基礎ボルト、インサート類等がある。
B コンクリート打込みに際しては、あらかじめアンカーの位置や方向等の精度を確保するように注意する。
(ii) あと施工アンカー工法
@ あと施工アンカーは、次の金属系アンカーと接着系アンカーとに大別される。
1) 金属系アンカー
躯体コンクリート面にドリル等で所定の孔をあけて金属拡張アンカーを挿入し、打撃又は回転締付けにより下部を機械的に拡張させてコンクリートに固着させる方式であり、「おねじ形」(本体とボルトが一体のもの)と「めねじ形」(本体とボルトが分離しているもの)があり、種類により工法及び耐力特性が著しく異なるので注意が必要である。
その形状の例を図14.1.1に、施工の例を図14.1.2に示す。
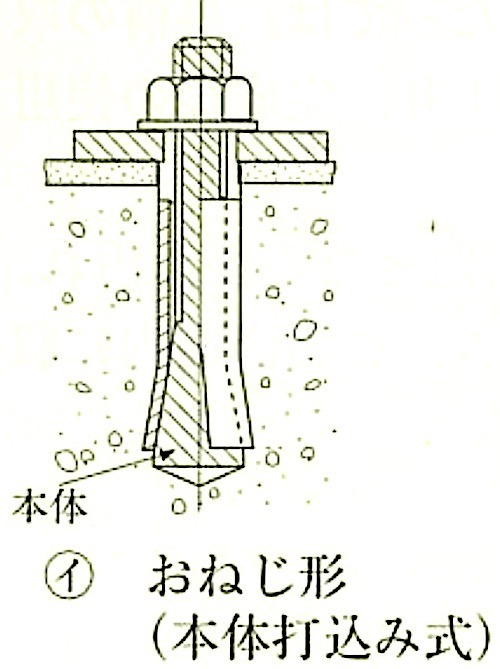
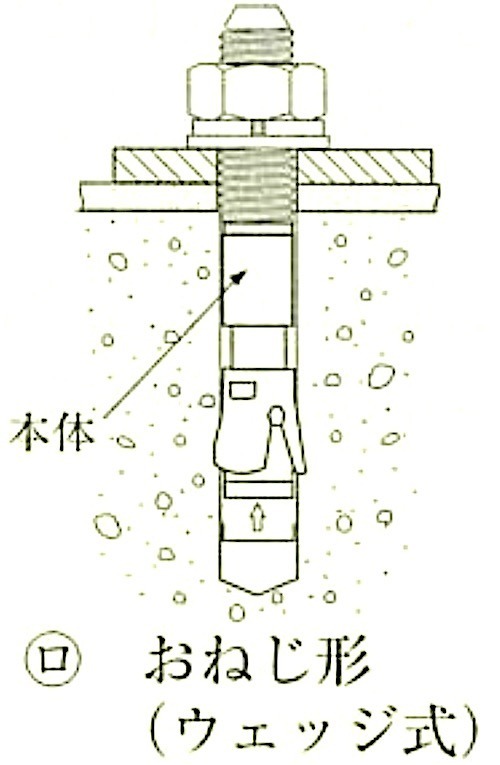
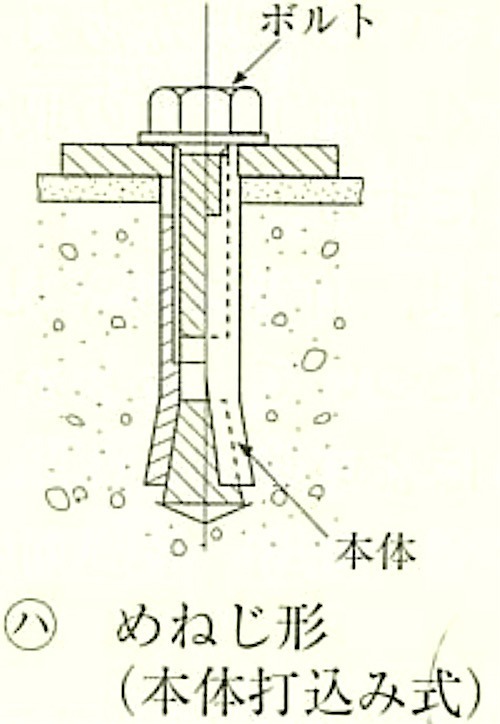
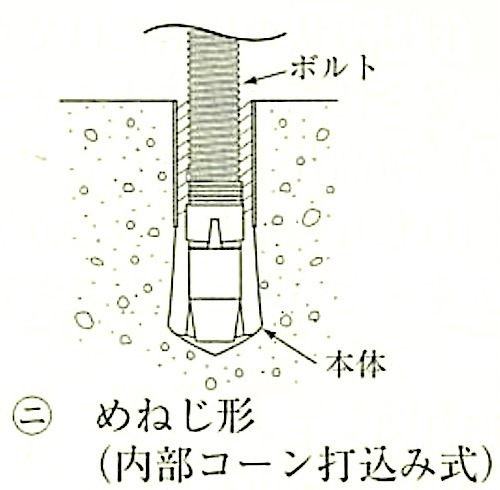
図14.1.1 金属系アンカーの形状の例
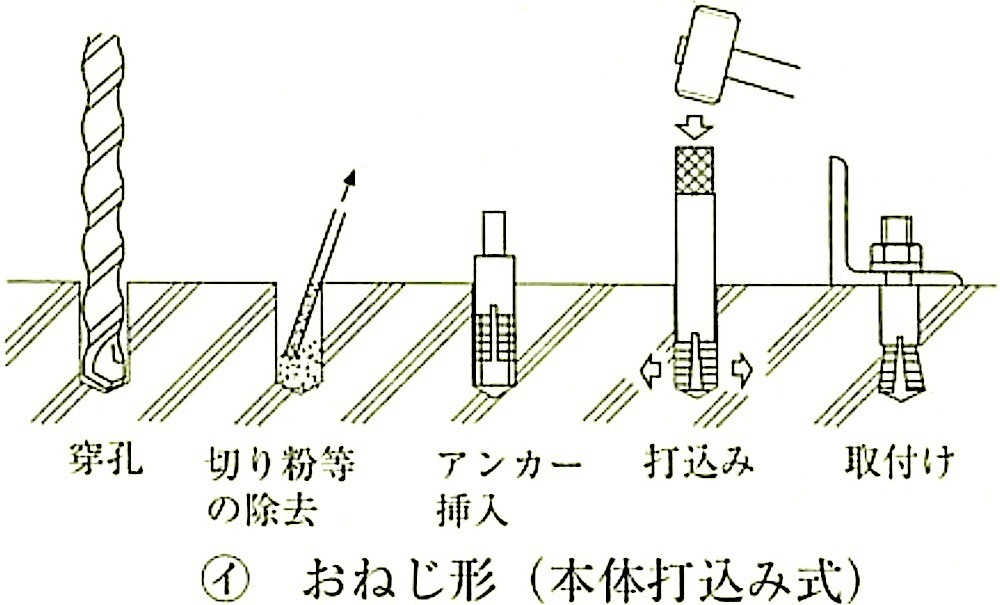
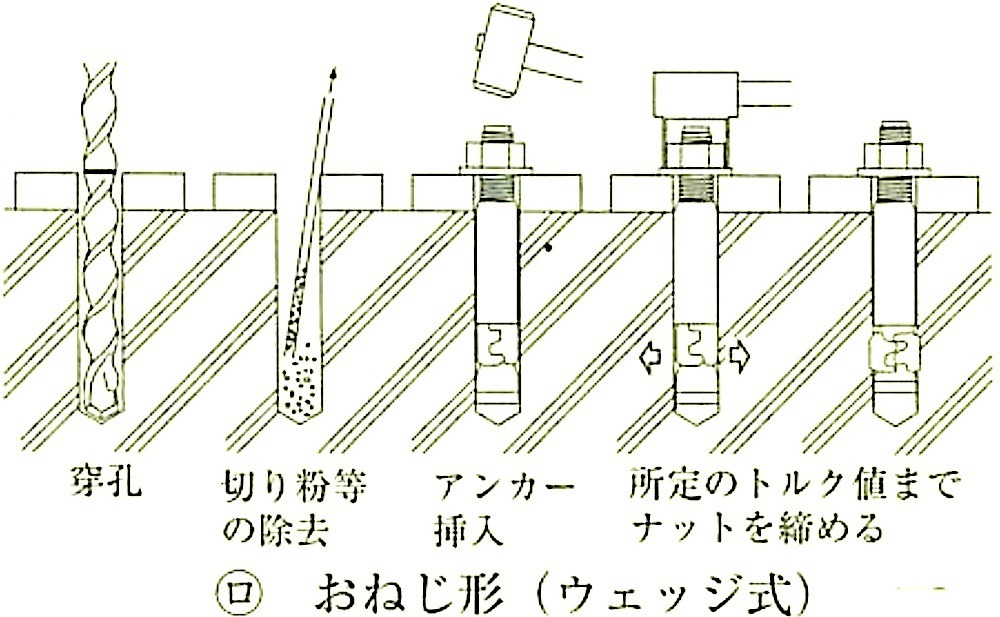
図14.1.2 金属系アンカーの施工の例
2) 接着系アンカー
躯体コンクリート面にドリル等で所定の孔をあけ、その内に接着剤を注入してアンカーボルトを埋め込む方法(注入型)と、孔内に樹脂及び硬化促進剤・骨材等を充填したガラス管のカプセルを挿入し、アンカーボルトをその上からハンマードリル等の回転打撃によって打ち込むことにより、接着剤の主成分(主剤)、硬化剤、骨材、粉砕されたガラス管等が混合されて硬化し、接着力によって固定される方法(カプセル型)がある。
接着系アンカーの留意事項等は、次のようなものである。
・接着材料には、ポリエステル系、エポキシアクリレート系(ビニルエステル系とも呼ぶ。)、ビニルウレタン系.エポキシ系樹脂等の有機系とセメント類の無機系とがある。
・金属拡張アンカーに比べ、一般に埋込み深さが確保されているので、引張耐力が大きい。
・耐熱性、耐火性又は耐薬品性が要求される部位に使用する場合には十分注意する。
・ 耐力の経年変化の有無については、製造所等のデータ等により十分検討する。
接着系アンカーの形状の例を図14.1.3に、その施工の例を図14.1.4に示す。
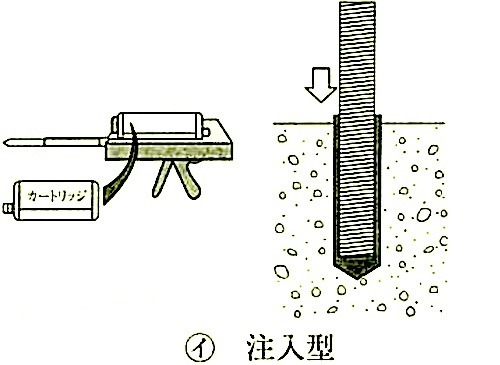
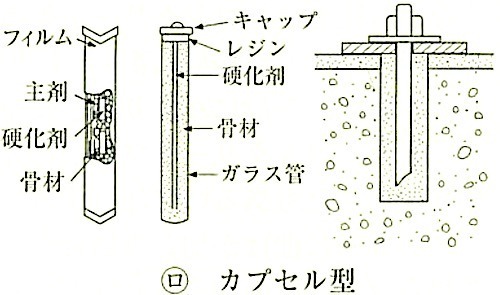
図14.1.3 接着系アンカーの形状の例
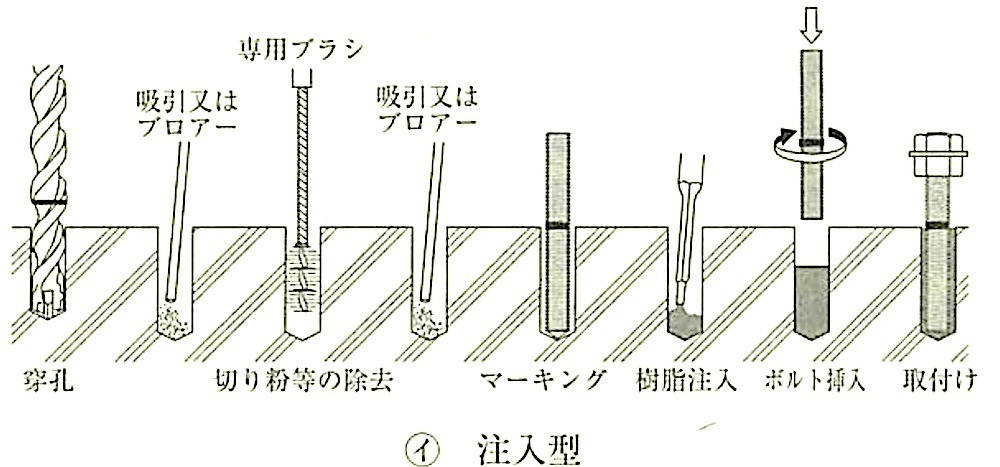
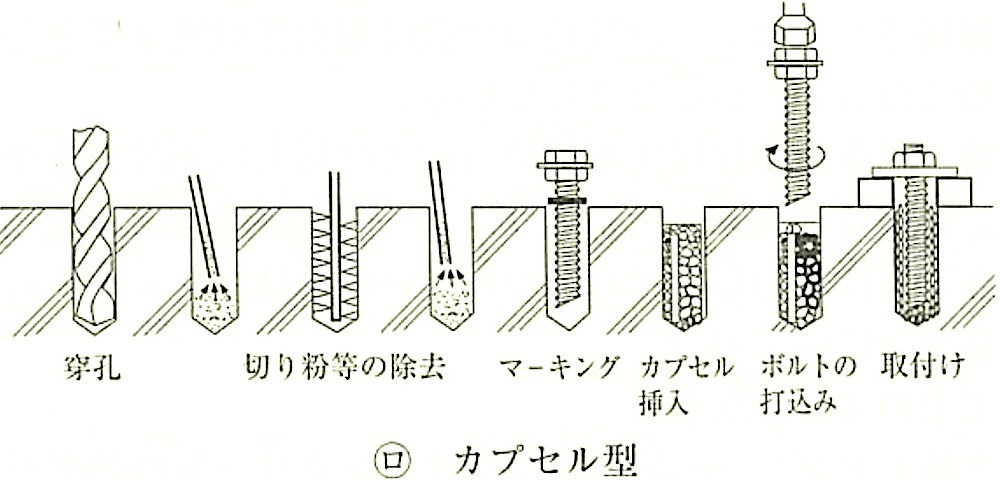
図14.1.4 接着系アンカーの施工の例
A 施工方法等
1) あと施工アンカー工法の開発・普及が進んできたことや必要な位置に正確に設置できることなどにより、近年、製品や内外装材の取付けのみでなく、重量物や既存建築物等における耐震補強部材の取付け等にも広く使用されるようになってきた。
「標仕」14.1.3(b)では、「あと施工アンカーの類とする場合は、十分耐カのあるものとする。」と規定している。通常、引抜き荷重の1/3 程度が設計用引張強度とされているが、躯体コンクリートの強度や施工品質等も踏まえて検討する必要がある。
2) あと施工アンカーの種類、耐力、断面寸法、間隔等の検討に当たっては、荷重条件等を整理し、設計用引張強度以下となるようにする。
なお、耐力は、コンクリート等の下地の状態、へりあき寸法、アンカーピッチ(間隔)、埋込み深さ等も重要な要素であり、適用部位や用途により異なるが、一般に、へりあき及び間隔は埋込み深さの2倍以上としている。また、コンクリートブロック等に設置する場合は、所要の耐力が期待できないこともあるので注意する。
3) アンカーに曲げが加わる場合や繰返し荷重や長時間にわたり振動を受ける場合等は、耐力が著しく低下することがあるので、必要に応じて設計担当者と打ち合わせて検討する。
4) あと施工アンカー工法とする場合は、防水層の貫通、埋込み配管等への損傷を与えないよう事前に対策を講ずる必要がある。
5) 「標仕」では、構造耐力又は安全上重要な部分に使用する場合には、特記により引抜き耐力の確認試験を行うこととしている。
試験箇所数は、1ロット当たり3本以上とする。
なお、確認試験を行うと特記された場合でも、構造耐力及び安全上から軽易と見なせるロットでは、試験を省略できるとしている。したがって、監督職員は、あと施工アンカーの取付け状況等を考慮して、安全性に問題がなければ試験を省略させてもよい。
6) 現場において引抜き耐力の確認試験を行い合格したものは、そのまま工事で採用されるため、試験荷重は設計用引張強度までとし、破壊に至るまでの加力は行わないこととしている。
7) 常時、引張力が作用する部位(例えば見上げ面等に施工する場合)において、引抜き方向にあと施工アンカーを適用することは避ける。ただし、引抜き方向に適用しなければならない場合は、フェールセーフを含めて安全性を十分に検討する。
8) 施工上の主な留意事項
あと施工アンカーの耐力は、躯体コンクリートの強度や施工品質に大きく左右されるため、次の事項に留意し、確実な施工管理を行わせる必要がある。
・ 所定のドリル径の選定及び穿孔深さの確保(ドリルにマーキングを施すなど)。
なお、モルタル等仕上材の厚さは,有効埋込み深さに含めない。
・穿孔内の清掃、異物の除去を確実に行う。
・躯体品質により、豆板等を有する場合は、その部位を避けて施工する。
・施工完了後全数について、目視による打込み代の確認、打撃音(手ごたえ)、締付けトルクによる確認等のほか、製造所等の指定する確認事項等を行う。
・接着系アンカーの場合は、施工中、接着材料の流動性、ボルトのマーキング、かくはん状態、接着材料の充填状態、ボルトの埋設状態等について確認する。
また、施工完了後自主検査を行う。自主検査項目は、目視、接触及び打音検査とする。
・あと施工アンカーの品質・性能を確保するためには、施工する技術者の技量等が重要である。これを維持・向上させるための一例として、(-社)日本建築あと施工アンカー協会では、平成8年から「あと施工アンカー技術者資格認定試験」を実施している。
(iii) 発射打込みびょう
「標仕」以外の工法として、発射打込みびょうがある。この工法はコンクリートや鋼材等に適応するびょう打ち機を用いて、空包(びょう打ち機用空包)の火薬の燃焼ガスにより打ち込むもので、びょう打ち機は「銃砲刀剣類所持等取締法」の適用を受け、空包は「火薬類取締法」による規制を受けており、所持及び使用に当たっては法令等に定められた手続きが必要である。
しかし、最近では、これら法令等に抵触しないガス式のびょう打ち機も使用されている。
1) びょう打ち機はその機構により、「高速式」(火薬のガスを直接びょうに作用させるもの)と「低速式」(銃口内にピストン等の中間機構を有するもので、下地に貫入する際の速度が比較的遅いもの)とがあるが、一般に建築の現場では「低速式」が用いられている。また、ガス式のびょう打ち機の機構も「低速式」である(図14.1.5参照)。
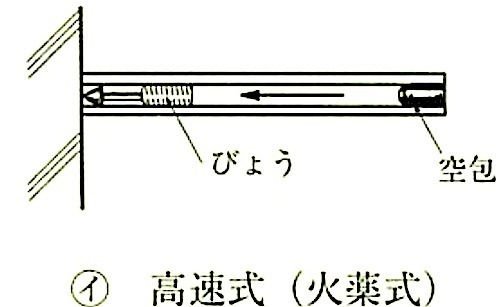
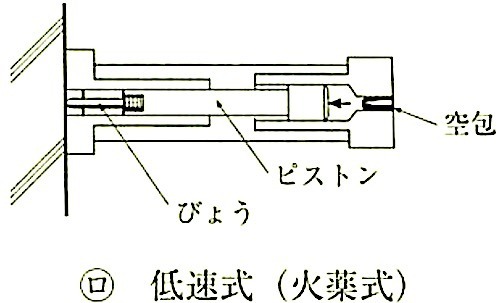
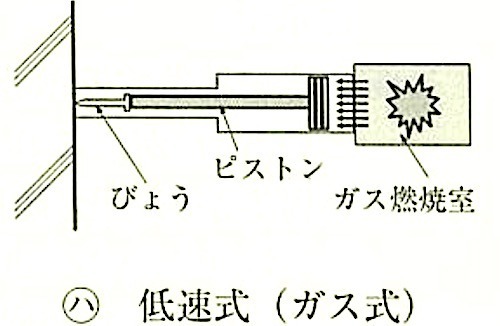
図14.1.5 びょう打ち機の機構
2) びょう打ち機の空包は、びょう打ち機の製造所が指定するものとする。
また、びょう打ち機には、各種防止装置や安全装置等が設けられているが、取扱いには注意する。
なお、空包の強さにより、弱・中・強等に分けられ、色で識別されている。
3) コンクリートに対する適正な貫入深さは、びょう軸径 27mm ±5mmで、それ以上深く貫入させてもびょうの固着力は大きくならない。
4) 施工上の主な留意事項
・下地の状況を確認する。特に材質と厚さに注意する。
・びょうが下地を貫通するおそれがある場合には、使用しない。
・改修工事等で既存のコンクリート、間仕切、スラブ等に施工する場合は下地の状態及び背後の状況を確認し、十分に安全性を確保する。
・コンクリートに打ち込む場合、端部の端空きは70mm以上、打込み間隔は80mm以上、母材厚100mm以上が原則とされている。
なお、同じ箇所に2度打ちしてはならない。
・取付け物ごとに群(複数本)による留付けを原則としている。
・びょう打ち機の取扱いについては、(公社) 全国火薬類保安協会「建設用びょう打ち銃、同空包の安全な取扱い」に、その要領が示されているので参考にするとよい。
(b) 金属の腐食と接触腐食防止方法
(1) 金属の腐食を大別すると次のようになる。
腐 食
湿食:接する環境に液体がある場合の腐食であり、200℃以下で起こる腐食はこれに属する。塩、亜硫酸ガス等は腐食を促進する。
乾食:接する環境に液体がなくても生じる腐食で、200℃以上でなければ生じない。
(2) 通常の腐食は、電解質の水溶液を電解液とする局部電池構成により電気分解を起こし、陽極側の金属が消耗する湿食である。
局部電池構成の原因は種々あるが、主なものは次のとおりである。
(i) 金属面の組成、組織その他の不均一性
(ii) 異種金属の接触(接触腐食という。)。異種金属には電極電位の相異があり、電位の差が大きければ腐食の進み方は早くなる。電極電位については表14.1.1に示す。
(iii) 水に溶解する酸素濃度の差。水面付近は、腐食が発生しやすい(通気差腐食 という。)がこれは酸素濃度の差が影響している。同様に、隙間あるいは深い傷等があると、隙間の底との濃度差により腐食が進行する(隙間腐食という。)。
表14.1.1 海水中における金属の電極電位(飽和廿しょう基準)
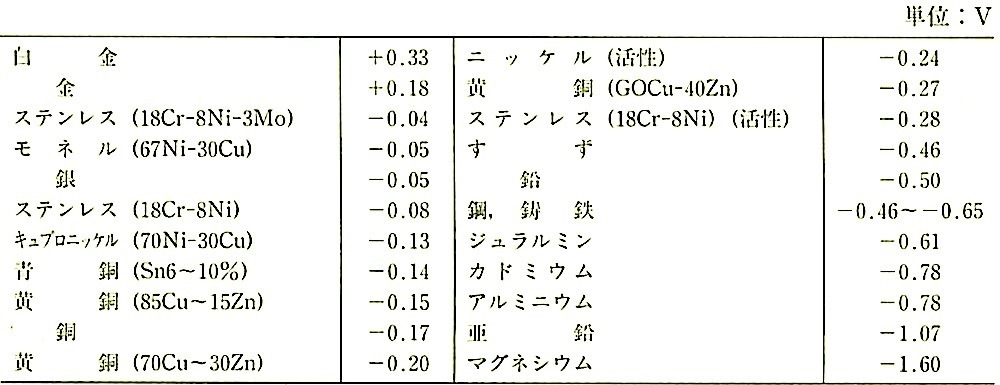
(3) 金属の接触腐食の防止のための処置
(i) 電極電位の差の小さい材料を選んで用いること。電極電位は環境条件等により変化するが表14.1.1を参考にするとよい。
(ii) 材料と材料の間に絶縁材を挿入する。
@ 軟鋼とアルミニウムの場合
1) 軟鋼を塗装等により絶縁する。
2) ポリサルファイド系のシーリング材を接合部にこて塗りすれば非常に効果がある。
A ステンレスと鋼又は銅合金の場合
塩化ビニル材等の絶縁材で一方を被覆するか、間に挟む、あるいは合わせ目の全周にわたってシーリング材で完全にシールする。
B アルミニウムと銅の場合
エポキシ系の塗料又はタールエポキシ系の塗料を塗り付ける。
(iii) アルミニウムとモルタルあるいは木材との接触腐食の防止
@ モルタルに使用する砂は塩分の少ないもの(NaCl換算で0.04%以下)を使用する。
A 木材は塩分や水分(含水率20%以下)の少ないものを使用する。
(c) 表面処理の下地処理
鋼及び亜鉛めっきの下地処理は、18章2節によるものとし、アルミニウムの下地処理は、14.2.2(b)(5)による。
14.1.4 養生その他
(a) 製品のほとんどの部分が工場で仕上げられているので、現場搬入に先立ち養生する必要がある。
「標仕」14.1.4(a)では、比較的使用頻度の高いポリエチレンフィルム及びはく離ペイントを挙げているが、その他の材料でも金物に適したものならばよい。
はく離ペイントはビニル系のものが多く、仕上げ面に塗り付けることにより薄い被覆で保護するが、不要になれば簡単にはがすことのできる塗料である。
(b) 現場に取り付けた製品には、それぞれに相応した養生が必要であるが、出隅等の損傷のおそれのある部分は、当て板、ダンボール紙等の適切な保護材を取り付けて養生するのがよい。
(c) 養生の必要がなくなったときには養生材は速かに取り除き、汚染等があれば清掃除去する。
(d) 装飾等の目的で、鏡面仕上げ等をしたものは、必要に応じてワックス等でふき上げてつや出しをする。
この場合、材種、仕上げ等によっては損傷を起こすこともあるので、専門業者に任せるのがよい。
(e) 部品類は、破損しないようにダンポール箱等に入れ、紛失するおそれのない場所に保管するのがよい。
14.1.5 金属材料の概要
(a) 一般事項
金属の形状、構成による分類を図14.1.6に示す。
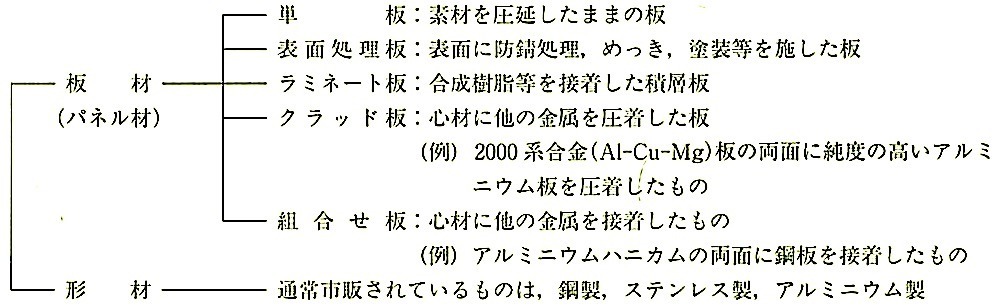
図14.1.6 金属の形状、構成による分類
(b) 鋼
(1) 金属工事に用いられる鉄は、ほとんど炭素鋼であり、炭素鋼は鉄を主とし、炭素の量によって主要な性質が支配される。
含まれる炭素量は、0.04〜2.1%であり、その他に少量のけい素(Si)、マンガン(Mn)、りん(P)、硫黄(S)を含んでいる。
(2) 鋼製品については、それぞれ次のJISに規定されている。
形鋼:JIS G 3101(一般構造用圧延錮材)、
JIS G 3350(7.11.2 (a)参照)
鋼板:JIS G 3101、JIS G 3141(冷間圧延鋼板及び鋼帯)
鋼管:JIS G 3444(一般構造用炭素鋼鋼管)、
JIS G 3466(一般構造用角形鋼管)
鉄筋:JIS G 3112(5.2.1参照)
溶融亜鉛めっき鋼板:JIS G 3302(溶融亜鉛めっき鋼板及び鋼帯)
溶融亜鉛アルミニウム合金めっき鋼板:
JIS G 3317(溶融亜鉛-5%アルミニウム合金めっき鋼板及び鋼帯)
溶融アルミニウム亜鉛合金めっき鋼板:
JIS G 3321(溶融55%アルミニウム-亜鉛合金めっき鋼板及び鋼帯)
(c) ステンレス
(1) ステンレスの種類
(i) 鉄(Fe)と11%以上のクロム(Cr)の合金をつくると外気中における耐食性が増すが、更にニッケルが添加されるといっそう耐食性を妍す。このような合金をステンレスという。
(ii) ステンレス製品については、それぞれ次のJISに規定されている。
ステンレス鋼管:JIS G 3446、JIS G 3448、JIS G 3459
ステンレス鋼板・帯:JIS G 3320、JIS G 4304、JIS G 4305
ステンレス条鋼:JIS G 4303、JIS G 4309、JIS G 4317、
JIS G 4318、JIS G 4320、JIS G 4321
代表的な冷間ステンレス鋼板及びステンレス鋼線材の化学成分等を表14.1.2に示す。
表14.1.2 冷間ステンレス鋼板及びステンレス鋼線材の化学成分等
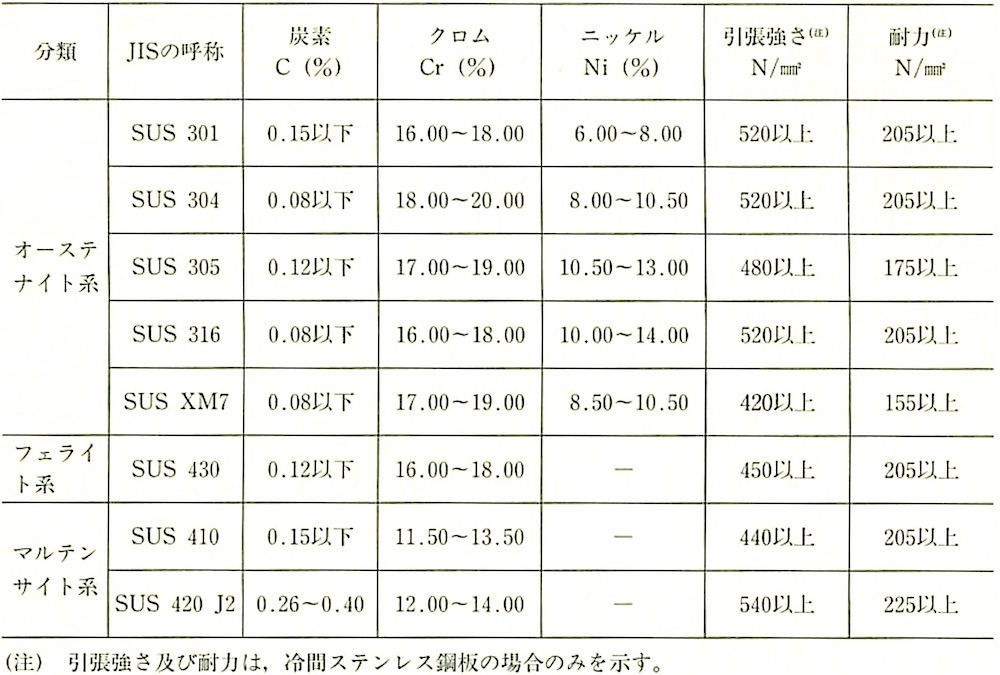
(iii) 各系の代表例を次に示す。
@ SUS 410〈13Cr〉:マルテンサイト系
やや焦味を帯びた感じで、ステンレス鋼としては比較的錆びやすい。加工性はやや良好であるが、溶接性は良くない。磁性があり磁石につく。
A SUS 430〈18Cr〉:フェライト系
建築関係でSUS 304についで使用されるステンレスである。マルテンサイト系よりやや白く、耐酸性が不十分で、大気中でも少しずつ錆びるので、海岸地方での外装には不向きである。溶接性は良いが、溶接部の耐食性が母材より著しく劣る。また、加工性はオーステナイト系より劣り、焼人れしても硬化しない。熱膨張係数が小である。新品ではオーステナイト系と見分けにくいが、磁性があるので磁石につくことで見分けられる。
B SUS 304〈18Cr-8Ni〉:オーステナイト系
建築関係で最もよく使用されるステンレスである。@及びAより銀白色である。Ni含有のため耐食性、耐熱性に優れている。加工性、溶接性とも良好で、高温時でも強度は大であり、焼入れしても硬化しない。原則として磁性はないが、加工法によっては結品構造が変わる(加工誘起変態を起こし、面心立方格子から体心立方格子に変化する。)場合もある。
C SUS 316〈18Cr-12Ni-2Mo〉:オーステナイト系
SUS 304とほとんど類似した特性をもつが、組成分としてモリブテンを加えている。海岸地方や工業地帯のように腐食要因の多い環境の建築物の外装や屋根材として、SUS 304より、やや耐食性のあるものとして使用する場合がある。
D SUS 305〈18Cr-12Ni-0.1C〉:オーステナイト系
SUS 304に比べ、加工硬化性が低い。へら絞り、特殊引抜き、冷間圧延に用いられる。
E SUS X M7〈18Cr-9Ni-3Cu〉:オーステナイト系
建築関係で小ねじ等によく使用されるステンレス鋼線材である。
SUS 304に銅(Cu)を添加して冷間加工性の向上を図ったものである。
(2) ステンレスの取扱い上の注意事項
(i) ステンレスは、比較的耐食性の高い金属ではあるが、必ずしも錆びないものではない。したがって、不適当な使い方をすれば、錆びることもあり次の事項には注意する必要がある。
@ 炭素鋼と接触させると、初めは炭素鋼が侵されるが、赤錆が発錆するとステンレスも侵される。
A 水のたまるような狭い隙間があると腐食が進む。これは、酸素が十分に行きわたらず、酸化皮膜が形成できないため、腐食しやすくなることによる。
B 銅合金と接触して腐食が始まると進み方が急速になる。
C 空気中の亜硫酸ガス、ばい煙の粒子、塩分等によっても腐食する。
(ii) ステンレスの汚れや鋳は、ほとんどの場合、鉄粉、塩分その他の異物の付着に起因するもらい錆である。したがって、鉄粉等が付着しそれが湿気を含んで赤錆状に広がらないうちに除去する。このため、特に錆びやすい環境で使用するステンレスの場合は、材質を考慮するとともにその納まりについても清掃しやすいよう配慮する必要がある。
(d) アルミニウム及びアルミニウム合金
(1) アルミニウム及びアルミニウム合金(以下、この章では「アルミニウム」という。)は、比重が2.7で鉄に比べ約1/3の軽い金属である。
表面は、銀白色で自然生成の酸化皮膜に保護されて美観を保つが、更にその性能を高め意匠性を付加させるために、陽極酸化処理や塗装等の表面処理が行われる。
アルミニウムの種類、化学成分、機械的性質(引張強さ、耐力、伸び等)について、板材はJIS H 4000(アルミニウム及びアルミニウム合金の板及び条)、形材はJIS H 4100(アルミニウム及びアルミニウム合金の押出形材)に定められている。
建築で用いる主なアルミニウムを表14.1.3に示す。
表14.1.3 建築で用いる主なアルミニウム及びアルミニウム合金
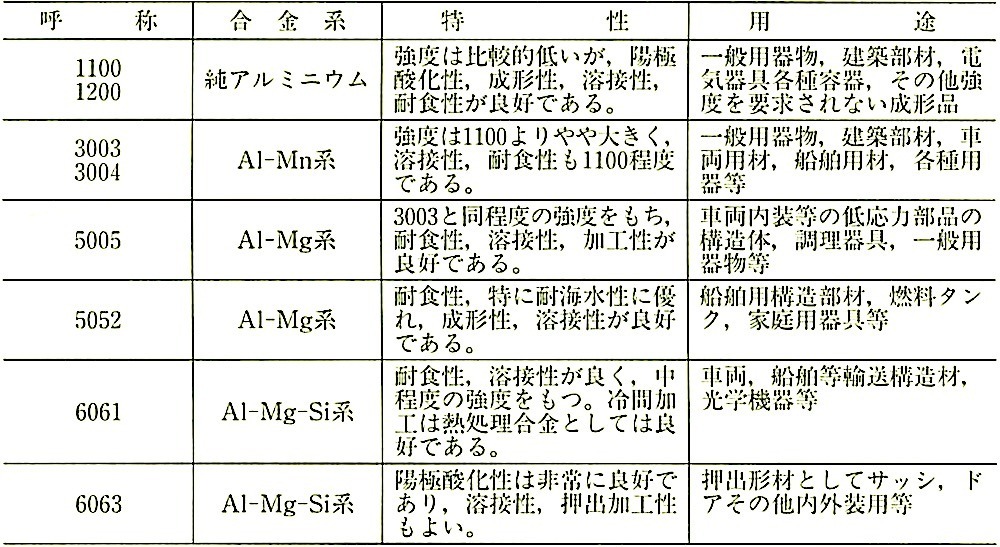
(2) アルミニウムは、熱処理、加工硬化により材質の機械的性質を調整(調質)し、使用目的に合わせることができる。JIS H 0001(アルミニウム、マグネシウム及びそれらの合金ー質別記号)では、これによる分類を定めている。
建材においては、板材類ではHタイプ、押出形材ではTタイプが多く使われる。アルミニウムの材質表示として板材ではA 1100 P-H14、押出形材ではA 6063 S-T5が代表的なものである。
ここでAに続く番号は、表14.1.3 の合金種類の呼称、Pは板材、Sは普通級精度の押出形材を示し、H14、T5 はJIS H 0001による細分記号を示しており、H14は加工硬化だけで1/2 硬質にしたもの、T5 は押出し後空冷し、その後人工時効硬化処理を施したものである。
(3) アルミニウムは、比較的耐食性に優れているが、酸、アルカリ及び塩素分の介在によって腐食しやすくなる。このため、アルミニウム建材には各種の表面処理が施される(2節参照)。
(4) アルミニウムは湿潤環境で異種金属と接触すると電気化学的な腐食を生じることがある。乾燥状態では通常の仕様により防止できるが、アルミニウム周囲のモルタルや木材が漏水や結露水等により湿潤状態が持続されると腐食を生じることがある。このとき含有する塩素が多いと腐食は促進する。
(5) アルミニウムは大気中の汚染物質により汚れ、そのまま放置すると外観が損なわれるとともに点食等の腐食を生じることがある。美観を維持し使用するためには定期的なメンテナンスを行うことが必要である。
(6) 製品の仕上り及び劣化状態を診断する場合、有害な傷や見え掛り部の使用上問題となる傷、汚れ、反り、へこみ等についてあらかじめ限度を定めておき、この限度内に収まっていることを考えればよい。これらの限度を定めるに当たり判断基準として建設大臣官房技術調査室監修「外装仕上げの耐久性向上技術」の診断方法を抜枠して次に示す。
第4編 アルミニウム合金製外装および開口部材
2.2 診断手法
i) 診断は、非専門家が判断しやすいように原則として「なし」「目立つ」の2段階評価とし、汚れのうちのしみ、きず、腐食のうちの点食、その他の腐食および塗膜劣化については「目立つ」「やや目立つ」および「なし」の3段階評価とし、視力1.0程度の者が目視で5mの距離から認められる程度を「目立つ」とし、1mの距離から認められる程度を「やや目立つ」とする。
ii) 劣化の評価は評価者の知識、目的意識など主観に依存しやすいが、これをなるべく客観的、定量的な評価を行えるようにした。
(e) 銅及び銅合金
(1) 銅は淡赤色であり、亜鉛、すず、アルミニウム等と合金を作ると黄色から金色になり、ニッケルとの合金は白色になる。
(2) 一般に建築で用いられている銅合金には、次のようなものがある。
(i) 丹銀
銅に 5〜20%の亜鉛を加えたものを丹銅という。
丹銅は、JIS H 3100(銅及び銅合金の板並びに条)のC 2100 〜 C 2400に定められている。このうち建築用としては C 2200、通称 9:1(くいち)丹銅が用いられる。プロンズ板というのは、ほとんどがこの丹銅板である。
(ii) 黄銅
銅に 30〜40%の亜鉛を加えたものを黄銅という。
通常、黄銅には亜鉛の含有量により7:3黄銅、65:35黄銅、6:4黄銅に区分されている。色は亜鉛が少ないものほど黄色が強い。亜鉛が増すに従って強度は高くなるが、加工性は劣る。用途として建築用では階段の手すり、建具金物、目地棒、内外装材及び建築装飾に用いられる。
なお、銅、丹銅及び黄銅の組成と色調との関係を図14.1.7に示す。
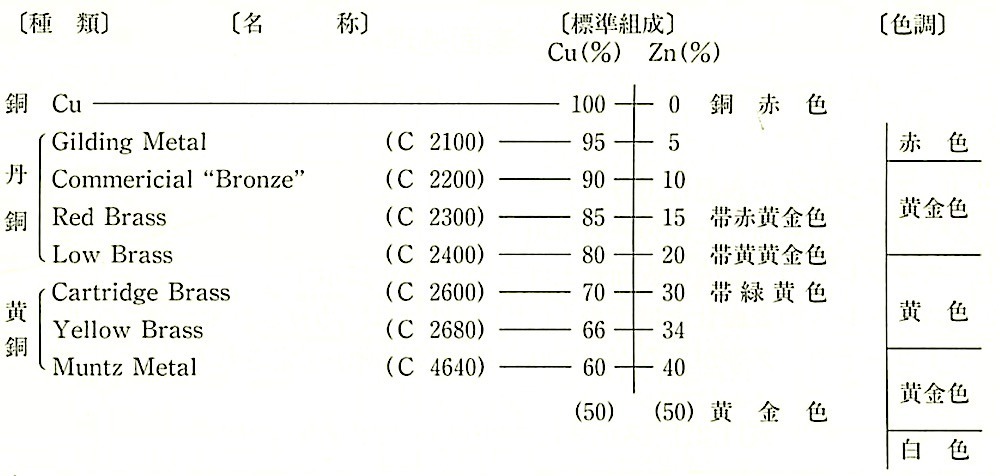
図14.1.7 銅、丹銅及び黄銅の組成と色調
(iii) 青銅
一般には、銅を主としてすずを加えたものを青銅という。
通常は、銅にすず 2〜11%と亜鉛及び鉛を加えたもので、給排水金具、建築用金具として用いられている。特殊な建築金物にりん青銅が用いられることもある。
一方、建築金物の業界では、(i) の丹銅、(ii)の黄銅を含めて「プロンズ」ということが多いので注意する必要がある。
(iv) 洋白〈ニッケルシルバー〉
銅にニッケルと亜鉛を加えた合金で、ニッケルの多いものは銀白色、少ないものは黄色を帯ぴた灰色になる。
「洋銀」とは洋白の別名で銀白色である。
(3) 銅合金の仕上げの種類及び方法について表14.1.4に示す。
表14.1.4 銅合金の仕上げ
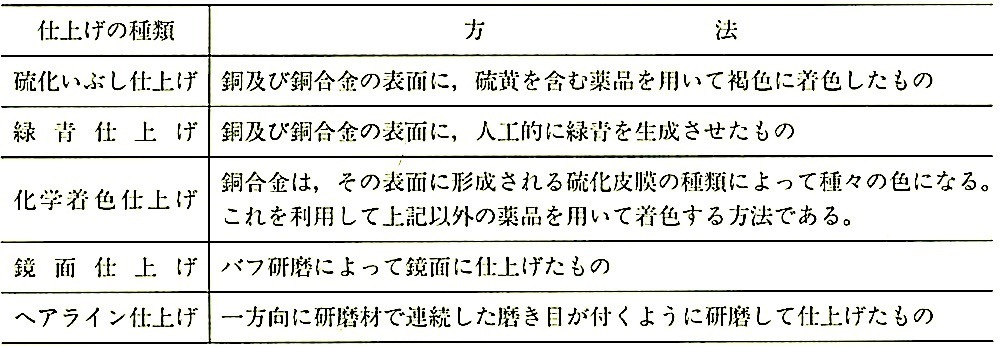