3節 工作一般
7.3.1 適用範囲
本節は、鉄骨の製作に係る工作一般、製作精度及び製品検査を対象としている。
7.3.2 工作図
(a) 工作図
(1) 工作図は、設計図書の内容を実現するに当たり製作・建方における指示書的な役割を果たすものであり、設計図書の記載内容を正しく織り込み、製作・建方が可能であることを確認したものでなければならない。施工性や構造細部の納まりの確認が工作図のみで困難な場合は現寸図・模型等を補助的に作成し確認する。
(2) 「標仕」1.2.3 (a)では、施工図等(工作図を含む。)については監督職員の承諾を受けることとしているので、鉄骨の製作・建方の工程に支障がでないように提出させる。
(3) 工作図は、監督職員・受注者等・鉄骨製作工場が協議確定した設計図書に関する疑義事項及び施工の手段・手法に関する提案事項を反映したものとする。
(4) 工作図は、軸組図・伏図・柱詳細図・梁詳細図・継手基準図、溶接基準図等で構成し、記載内容は次のとおりである。
i) 鉄骨部材の詳細な形状・寸法・材質・製品数量・製品符号
(ii) 溶接及び高カボルト接合部の形状・寸法・ボルトの種類・等級・継手符号
(iii) 設備関係・内外装関係付属金物、仮設金物、コンクリート関係・鉄筋関係孔、ファスナー類
(5) 工作図の検討事項は、次のとおりであり、工場製作や工事現場施工においてトラブルが生じないように十分な検討を行う。
(i) 柱・梁・工場組立部材等の符号(建物の通り符号を利用する場合や通し番号による場合が多い。)
(ii) 建物の基準線と鉄骨の基準線との関係
(iii) スパン(梁間)、階高等の基準寸法・基準線と柱・梁・工場組立部材等との位置関係、床からベースプレート下端までの寸法
(iv) 柱・梁・工場組立部材等の形状・寸法及び構成部材の形状・寸法
(v) 各部の部分的詳細
@柱と梁の取合い
A ベース回りの納まり
B スリーブ貫通部の補強等、また、隣接部材の接近のために、作業空間が狭く、ボルト締付け・溶接等の作業が困難な箇所の発見と処置
(iv) 接合部の添え板(スプライスプレート)・フィラープレート・クリアランス等及び次の@からCの事項に関する設計図書との照合
@ 高カボルトの種類・径・本数・ゲージ・ボルト間隔・最小縁端距離等
A 溶接の種類・開先形状・大きさと寸法・長さ・位置等
B アンカーボルトの種類・径・長さ・本数・位置等
C SRC造の場合の鉄筋工事との関係
また、高カボルト及び普通ボルトの縁端距離等を確認する場合は(c)(4)〜(6)を参照する。
(vii) 他の建築工事との関連
@ 内外装材料との関係
A 建具類の埋込み金物の納まり、特にフロアーヒンジ・シャッターケース等
B コンクリートの充填性を考慮した空気孔の設置等
C SRC造の場合の鉄筋工事との関係
(G) 仮設工事との関連
@ クレーンの設置、重量物の積載、風・地震に対する倒壊防止、土圧に対する支持等のために鉄骨を補強する場合は、設計担当者と打ち合わせる。
A 安全タラップ・吊りピース・足場用ピース・建入れ直し用ピース・親綱掛け用ピース等の仮設用金物の必要性
B ウェブ板厚が薄く、溶接・運搬・建方の際に変形のおそれがある場合、溶接組立上必要な場合、又は施工上タラップとして必要な場合を除き、原則としてバンドプレートは取り付けない。
(ix) 設備工事との関連
@ 主に、スリーブ位置、大きさ及び間隔の確認をする。(構造耐力上の制約についても確認する。)
A ダクト、配符等の系統を確認し、スリーブの数、大きさ等が不足しないようにする。
B 鉄骨の近くで交差する配管等の系統は、保温被覆材を含めて、施工性を確認する。
C 排水管等一定の勾配を必要とするもの、柱・梁の近くで方向を変えるものは特に注意する。
D ウェブ貫通孔板厚部分の耐火被覆材の厚さと保温被覆材を考慮した配管径の関係を確認する。
(b) 現 寸
(1) 鉄骨製作工場では、工作図のみでは不足する製作情報を作業者に伝える手段として、また、工場製作の能率向上を目的に現寸作業を行う。この現寸作業では、実物と同一寸法の定規(シナイ)・型板(フィルム)を作成する。一般には定規・型板の作成は、完備されている工作図から直接読み取り、作業をする方法が採用されており、標準的形状の建築物の場合、実物大の床書き現寸図については、通常作成する必要はない。
(2) 次のような場合は床書き現寸図やCADシステムから出力される実寸大のフィルムで作業性等を検討するのがよい。
(i) 曲率や90° 以外の取合い角度を有する変形した建築構造物の場合
(ii) 溶接作業及び高カボルトの締付けが困難と判断される箇所が存在する場合
(iii) 納まりが複雑で工作図からの直接読取りが困難な箇所が存在する場合
(3) NC(数値制御)加工装置を用いてけがき・切断・孔あけを行う場合は、定規・型板の作成に代わって、加工データが作成される。
(c) 「標仕」7.3.2 (b)では、高カボルト、普通ボルト及びアンカーボルトの縁端距離、ボルト間隔、ゲージ等は特記事項となっている。参考として、高力ボルト及び普通ボルトのゲージ、ボルト間隔、最小縁端距離等の標準を(1)から(6)までに示す。
(1) ボルトの表示記号の例を表7.3.1に示す。
表7.3.1 ボルトの表示記号の例
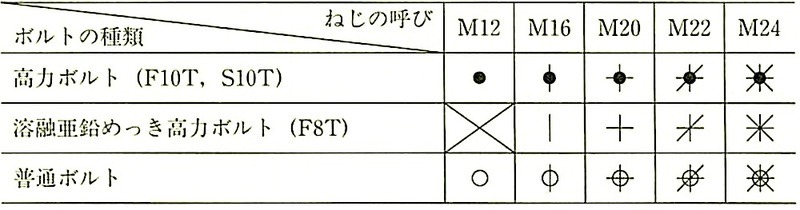
(2) ボルト孔の径を表7.3.2に示す。(「標仕」表7.3.2参照)
表7.3.2 ボルト孔の径 (単位:mm)
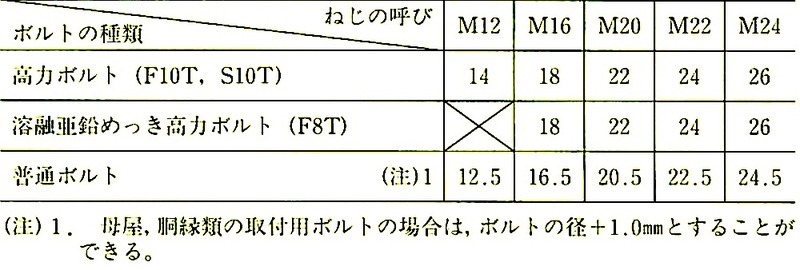
(3) 高カボルトの締付け長さに加える長さを表7.3.3に示す。(「標仕」表7.2.2参照)
表7.3.3 高力ボルトの締付け長さに加える長さ (単位:mm)
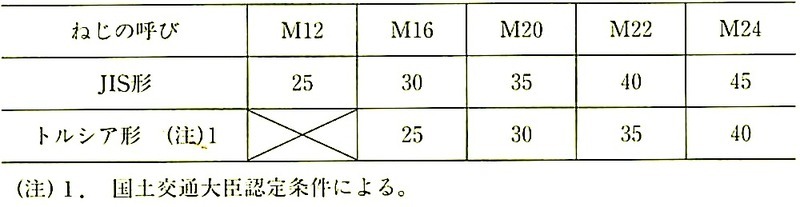
(4) 縁端距離及びボルト間隔を表7.3.4に示す。
表7.3.4 縁端距離及びボルト間隔(単位:mm)
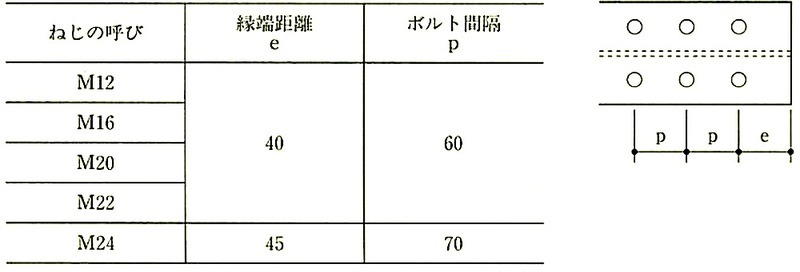
(5) 千烏打ちのゲージ及びボルト間隔を表7.3.5に示す。
表7.3.5 千烏打ちのゲージ及びボルト間隔(単位:mm)
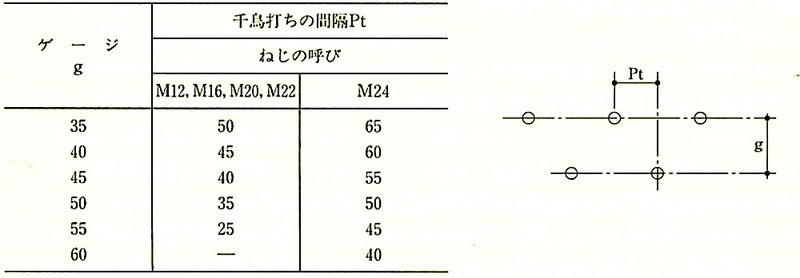
(6) 形鋼のゲージ及びボルトの最大軸径を表7.3.6に示す。
表7.3.6 形鋼のゲージ及びボルトの最大軸径
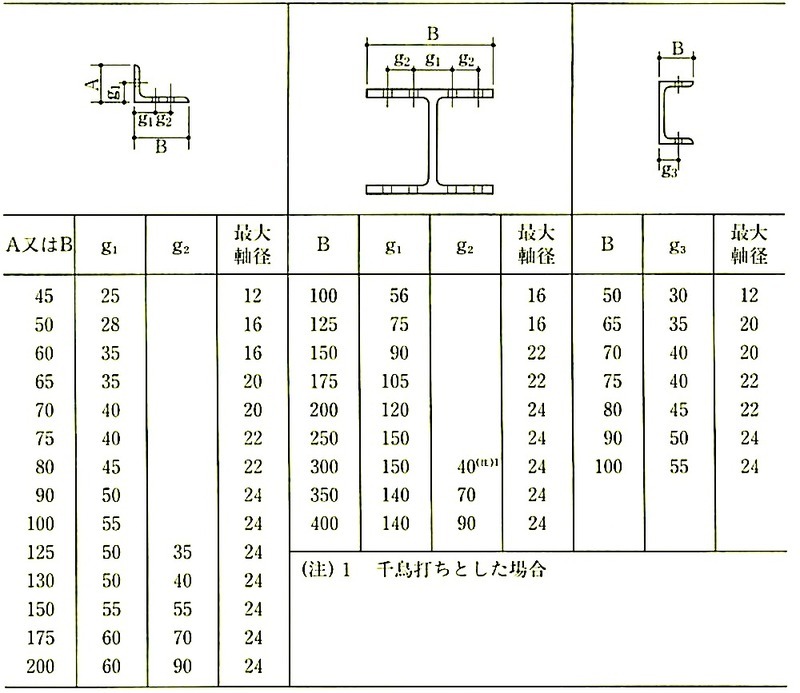
(7) (4)から(6)までの値は標準であり、高カボルト及び普通ボルトの縁端距離を変更する必要がある場合は、「鉄骨造の継手又は仕口の構造方法を定める件」(平成12年5月31日 建設省告示策1464号)に規定される値を下回らないようにしなければならない。
アンカーボルトの縁端距離は、「鉄骨造の柱の脚部を基礎に緊結する構造方法の基準を定める件」(平成12年5月31日 建設省告示第1456号)に定められているので、変更を行う場合はこの規定値を下回らないようにしなければならない。
(i) 図7.3.1のように配置されたボルトは、締付け機器の形によって、標準ピッチのままでは締付け機器が直角方向のボルトに当たって施工困難となることがある。
(ii) 部材が接近している場合には、締付け機器が入らないとか、トルクレンチのような長い締付け機器が動かせないことがある。(図7.3.2参照)

図 7.3.1 直交するボルトの締付け
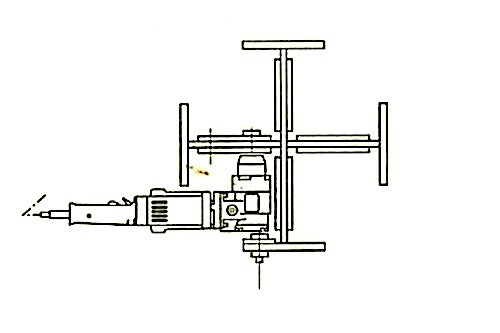
図 7.3.2 締付け機器の大きさの検討
7.3.3 製作精度
鉄骨の製作にかかる精度及び製品精度は、「標仕」7.3.3では、JASS 6付則6[鉄骨精度検査基準]によるとしている(7.13.1参照)。
なお、JASS 6では次に示すものには適用しないとしている。
(1) 特記による場合または工事監理者の認めた場合
(2) 特に精度を必要とする構造物あるいは構造物の部分
(3) 軽微な構造物あるいは構造物の部分
(4) 日本工業規格で定められた鋼材の寸法許容差
(5) その他、別に定められた寸法許容差
7.3.4 けがき
けがきは、工作図又は型板・定規等により、加工・組立時の情報を直接鋼材上に記入する作業である。
一般に墨差し・水糸等を用いるが、目的に応じけがき針・ポンチ・たがねを使用することもある。最近では、自動けがき装置が使用される場合もある。
しかし、けがき作業に使用するポンチやたがね等による打痕は、応力集中を招くことから鋼材の耐力を著しく低下させる原因となる。そのため「標仕」7.3.4(b)では、溶接により溶融する箇所又は切断、切削及び孔あけにより除去される箇所を除き、高張力鋼、曲げ加工される外側へのポンチによるけがきやたがね等で傷をつけることを禁止している。
けがき寸法は、製作中に生ずる収縮や変形等を考慮した値とする。また、あと工程の作業者に製作情報が正確に伝わるように、工事名略号、材質、加工情報等が明瞭に記入されていなければならない。
7.3.5 切断及び曲げ加工
(a) 素材切断面の直角度の許容差は、JASS 6付則6付表(11)による。(7.13.1参照)
(b) 切断方法には次のようなものがある。
(1) 機械切断法
(i) せん断によるもの
切断速度は速いが、短所として切断面でのまくれ・かえり等の発生、板の変形、切断面の硬化等の問題があり、「標仕」7.3.5 (a)(3)では適用範囲を13mm以下に限定し、更に主要部材の自由端及び溶接接合部への適用を禁止している。
なお、主要部材の自由端とは、梁や柱のフランジのへり等である。
(ii) 切削によるもの
切断線を削りとることで切断する方法で、次の方法がある。
1) のこぎり切断によるもの
バンドソーやコールドソーがあり、前者は切断速度はやや速く精度はよく斜め切りができ、後者は切断速度は近いが高い精度が得られる。
2) 砥石切断によるもの
切断速度は速く、丸鋼、角鋼、軽量形鋼等の切断に用いられる。
(2) ガス切断法
鉄と酸索の急激な化学反応を利用した切断法であり、機器としては手動ガス切断機、自動ガス切断機。形鋼切断機、鋼管切断機、フレームプレーナ、NC切断機等がある。また、手動ガス切断機にアタッチメント、ガイドを取り付け半自動装置として使用することもできる。切断速度は遅いが、最もよく使用されている。切断面の精度も良く、経済的である。
(3) プラズマ切断法
プラズマアークの熱及び気流を利用した切断法であり、適用板厚は0.5〜50 mm程度である。切断速度は速いが切断溝幅が大きい。
(4) レーザー切断法
光エネルギーの集光熱による切断法であり、適用可能板厚は 0.1〜25mm程度である。高速切断が可能で切断溝幅が狭く孔あけ加工が可能である。
(c) 切断面の許容差は、JASS 6付則6付表1 (9)・(10)による。(7.13.1参照)凹凸、ノッチ等の不良箇所はグラインダー等で修正する。特にやむを得ない理由から手動でガス切断した場合には、切断面の精度を確保することが困難であるため、注意する必要がある。
(d) 切断面のうちメタルタッチが指定されている部分は、フェーシングマシン又はロータリープレーナ等の切削加工機を使用し、仕上げ加工面が50μmRz程度、直角度が 1.5/1,000 以下になるように平滑に仕上げる。
(e) 切断加工(シャーリング工場での切断材も含む。)後の鋼材の材質確認は、識別色、識別マークの表示、あるいはマーキング(7.2.1 (b)(9)参照)による。
なお、JIS G 3136(建築構造用圧延鋼材)によるSN材の識別は、7.14.3 [ SN鋼材材質識別表示記号・位置及び鋼材の識別表示標準]によることもできる。
(f) 曲げ加工は鋼材の機械的性質等を損なわない方法で行う。次に示す平成12年建設省告示第2464号では、500℃以下の加熱、厚さ 6mm以上の鋼材等(鋳鉄及び鉄筋を除く。)の曲げ加工においては外側曲げ半径が材厚の10倍以上の場合は加工前後で同じ基準強度及び材料強度としてよいとしている。したがって、この範囲外で曲げ加工を行う場合は、加工後の機械的性質等が加工前の機械的性質等と同等以上であることを確認しなければならない。
ただし、200〜400℃の範囲は青熱脆性域といわれ鋼材が常温よりもろくなる。加熱曲げ加工を行う場合はこの範囲を絶対に避けなければならない(図7.2.3参照)。
(平成12年12月26日 建設省告示第2464号 最終改正 平成19年5月18日 )
第1 鋼材等の許容応力度の基準強度
一 鋼材等の許容応力度の基準強度は、次号に定めるもののほか、次の表の数値とする。
(表省略)
二 建築基準法第37条第一号の国土交通大臣の指定するJISに適合するもののうち前号の表に掲げる種類以外の鋼材等及び同条第二号の国土交通大臣の認定を受けた鋼材等の許容応力度の基準強度は、その種類及び品質に応じてそれぞれ国土交通大臣が指定した数値とする。
三 前2号の場合において、鋼材等を加工する場合には、加工後の当該鋼材等の機械的性質、化学成分その他の品質が加工前の当該鋼材等の機械的性質、化学成分その他の品質と同等以上であることを確かめなければならない。ただし、次のイからハまでのいずれかに該当する場合は、この限りでない。
イ.切断、溶接、局部的な加熱、鉄筋の曲げ加工その他の構造耐力上支障がない加工を行うとき。
ロ.摂氏500度以下の加熱を行うとき。
ハ.鋼材等(鋳鉄及び鉄筋を除く。以下ハにおいて同じ。)の曲げ加工(厚さが6mm以上の鋼材等の曲げ加工にあっては、外側曲げ半径が当該鋼材の厚さの10倍以上となるものに限る。)を行うとき。
第2 溶接部の許容応力度の基準強度
(省略)
第3 鋼材等の材料強度の基準強度
一.(省略)
二.(省略)
三.第1第三号の規定は、前2号の場合に準用する。
第4 溶接部の材料強度の基準強度
(省略)
(g) 曲げると外側は伸び、内側は縮むが、形鋼のようなものは曲げ角度が大きくなるとその影響が著しくなるので図7.3.3のように切曲げとするのがよい。ただし、曲げ半径は (f) による。
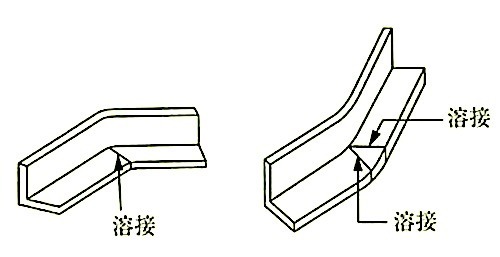
図7.3.3 形鋼の切曲げ加工
(h) H形断面材の材端部の開先、スカラップ加工は.7.6.4(a)及び7.6.5 (b)による。
7.3.6 ひずみの矯正
(a) ひずみの矯正は、常温若しくは局部加熱して行う。
(b) 400N/mm2、490N/mm2 級鋼材を局部加熱で矯正する場合の温度範囲は、次を標準とする。これ以外の鋼について、設計担当者と打ち合わせる。
(1) 加熱後空冷する場合 850~900℃
(2) 加熱後直ちに水冷する場合 600~650℃
(3) 空冷後水冷する場合 850~900℃
(ただし.水冷開始温度650℃以下)
なお、この温度は、加熱表面の温度を示している。温度測定には、接触温度計等が用いられる。
7.3.7 鉄筋の貫通孔径
(a) 鉄骨鉄筋コンクリート造では、鉄骨製作の段階で、鉄筋の買通孔をあけておかなければならない場合がある。
(b) 貫通孔径は、「標仕」表7.3.1による。
鉄筋が斜めに貫通する場合や鉄骨の形が複雑な場合には貫通孔の径を増す必要があるが、鉄筋の間隔によっては鉄骨の断面欠担が大きくなり、構造上問題となることがあるため、必要に応じて設計担当者と打ち合わせる。
なお、同一の部位に種々の径がある場合には、混同しやすいのでなるべく統一するのがよいが、その場合は、必ず設計担当者と打ち合わせる。
(c) 鉄筋の貫通孔の位置を決めるには、仕口部分の鉄筋の状態が分かっていなければならないが、簡単な場合の例を示せば図7.3.4のようになる。
図7.3.4 の作成に当たっての主な注意事項を次に示す。
(1) 鉄筋の交差位置では、どちら方向の鉄筋を上にするか決めなければならない。
一般的な基準はないが、通常梁せいの小さい方の主筋を外側にするなどの配慮が必要である。
(2) 四隅の梁筋の位置は、図7.3.4(ハ)の梁部分詳細に示すようにして定める。梁筋の仮想の直径 dを下式の値とする。
d ≦ 公称直径+節の最小高さ × 2
梁筋が2段になる場合は、内側になる鉄筋が特に鉄骨に当たりやすい。
(3) 鉄骨面と平行となる鉄筋の間隔は「標仕」5.3.5(d)及び(e)に定める鉄筋の間隔以上にする。
(4) 加工した鉄筋を、どのようにして差し込んだらよいか検討しながら鉄筋の位置及び継手位置等を定める。特に最外端の梁筋は注意を必要とする。
(5) 鉄骨フランジの鉄筋貫通は、耐力低下を招くので行ってはならない。
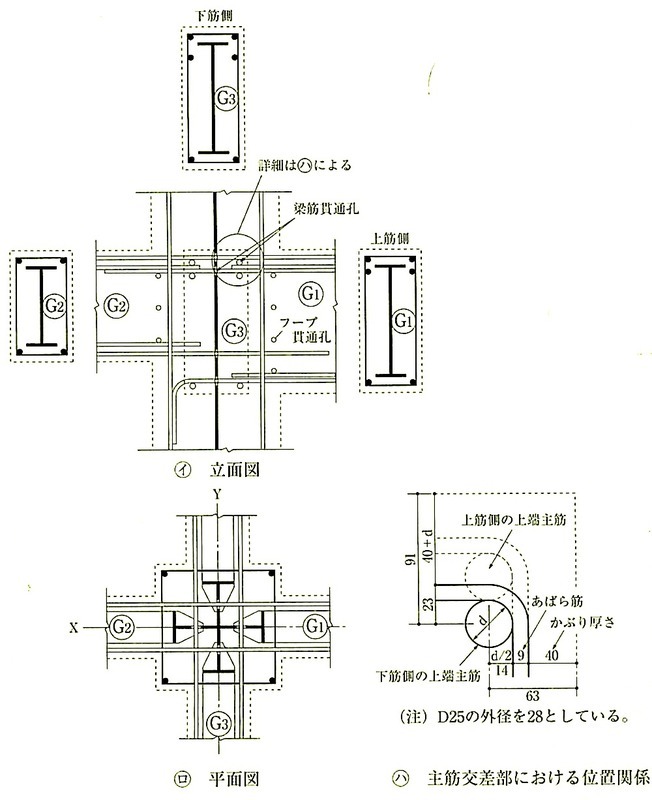
図7.3.4 仕口部分の梁筋貫通孔の例
7.3.8 ボルト孔
(a) 高カボルト用の孔あけ加工は、鉄骨製作工場で行い、ドリルあけとする。加工精度の確保が可能なことを工場製作要領書の提出等によって確認できる場合は、小・中形山形鋼等にせん断孔あけを使用することができる。高カボルト接合面をブラスト処理する場合は、ブラスト前に孔あけ加工を行う。
(b) ボルト孔、アンカーボルト孔、鉄筋貫通孔は、ドリルあけを原則とするが、板厚 13mm以下の場合は、せん断孔あけとすることができる。
(c) 設備配管用貫通孔、付属金物等の孔で、孔径が 30mm以上の場合はガス孔あけを使用できる。ガス孔あけを行う場合の切断面の粗さは100mRz以下、ノッチ深さは1mm以下とし、孔径の精度は ± 2mm以下とする。
(d) 高力ボルト、普通ボルト及びアンカーボルトの公称軸径に対する孔径は、「標仕」表7.3.2による。溶融亜鉛めっき高カボルトの公称軸径に対する孔径は表7.3.2による。
(e) 孔あけ加工は、孔あけされる部材表面に対して直角度を保ち、正規の位置に行う。ドリル孔あけ後の孔周辺のばり、切り粉、せん断孔あけ後のばり、まくれ及びガス孔あけ後の凹凸.ノッチはグラインダー等により除去する。
7.3.9 仮設用部材の取付け等
仮設用部材のほか、設備関係、コンクリート・鉄筋関係、内・外装関係等の付属金物類や付属金物をあと付けするための金物類の取付けには主に隅肉溶接が用いられるが、この隅肉溶接は「仮付け溶接」と称されることが多く、安易に施工されがちである。したがって、その取付けは作業環境が悪く溶接品質の確保が困難な工事現場を極力避け、可能な限り鉄骨製作工場で行う。ただし、製品完成後に鉄骨製作工場の屋外滞貨場で溶接した場合には、工事現場の作業環境とほとんど変わらない。それを避けるためには、製作工程に合わせた適切な時期に付属金物類の取付け要領を決定し、本体の工場製作と同時に付属金物類の取付けを行うことが必要である。このために、仮設用部材・付属金物類の取付けに関しては、施工図・工作図の作成段階に必要なものを盛り込んでおく必要がある。
やむを得ず工事現場で溶接する場合も、原則として、JIS Z 3801又は3841の有資格者が従事し、ショートビードを避けるほか、外観検査の実施等、主要部材の溶接と同等の品質が得られるように施工することが必要である。
7.3.10 仮 組
(a) 一般の建築鉄骨では例が少ないが、仮組の実施が特記されている場合には、仮組要領書を提出させ、特記内容と照合・確認する。
仮組を行う目的の主なものは、次のとおりである。
(1) 部材数が多く、製品精度が工事現場の出来形に影響を及ぼす場合
(2) 複雑な構造物で、工事現場の作業に支障がないことを確認しなければならない場合
(3) 大架構部材のたわみ量を工事現場の建方以前に確認しておく必要がある場合
(4) 遠隔地や交通が不便な土地で、不具合が発生したとき補修に多大な費用を要する場合
(5) 鉄道線路等に近接した工事現場のため、建方時間に制約を受ける場合
(b) 仮組要領書の主な記載内容は、次のとおりである。
(1) 仮組の範囲
仮組の目的、工場敷地、設備能力等から総合的に決定される。
(2) 仮組の方法
(i) たわみ量の測定が目的の場合は、工事現場の建方と同一条件になる方法を採用する。
(ii) 寸法精度・納まりの確認の場合は、分割や横転の方法等により、安全と作業性を考慮した方法を採用する。
(3) 確認項目・測定方法及び許容差
仮組における確認項目を次に示す。許容差はJASS 6付則6を参考にし、規定がないものはあらかじめ受注者等・鉄骨製作工場と打合せをしておく必要がある (7.13.1参照)。
@ 全体寸法
A 部材相互の接合部納まり
B 部材組立の可否
C たわみ量
7.3.11 巻 尺
(a) 鋼製巻尺は、JIS B 7512(鋼製巻尺)の1級品を使用する。
(b) 鉄骨工事では、工事現場と鉄骨製作工場で異なる基準巻尺を使用することから、双方の基準巻尺を照合し、その誤差が工事に支障のないことを確認しなければならない。確認は工事現場用と鉄骨製作用の基準巻尺を並べた状態で一定の張力(鋼製巻尺に指定された張力とする。一般には50N)を与え、基準巻尺間の目盛り差を読み取って行う。JIS 1級構製巻尺の長さ10mにおける最大許容差は ± 1.2mmである。したがって、長さにおいて最大相対誤差が2.4mmとなる場合が生じる。
(c) 工場製作の各工程において使用する鋼製巻尺は、鉄骨製作用基準巻尺と照合し、その誤差を確認する。使用する鋼製巻尺は、誤差が最大許容差の1/2程度の精度を有するものを選択して使用するのが望ましい。(2.2.3(d)参照)
(d) 工事現場で鋼製巻尺を使用する場合は、気温による鋼製巻尺の伸縮を考慮して測定時刻を定めるか、気温変化による温度補正を行う必要がある。(2.2.3(d)参照)
7.3.12 製品検査
(a) 受注者等及び鉄骨製作工場が実施している製品検査の内容は、次のようなものである。鉄骨製作工場の行う社内検査、受注者等の行う中間検査・受入検査については、7.1.5(b)を参照のこと。また、受注者等が行う受入検査には書類検査と対物検査がある。
(1) 形状及び寸法精度の検査
製品寸法について、所定の形状及び寸法精度であることを確認する検査であり、検査項目・方法・許容差はJASS 6付則6等を基に、工場製作要領書等で定められた値によって行う。 (7.13.1参照)
(2) 取合い部の検査
仕口部・取合いプレートについて、設計図書の指示通りであるかを確認する検査である。
(3) 外観の検査
部材表面・切断面・工事現場溶接部の開先について、傷・ノッチ等の有無を確認する検査であり、検査項目・方法・許容差は「標仕」の規定のほか、7.3.5、7.6.7、7.6.10を参考にする。
(4) 高カボルト接合面の検査
高カボルト接合面について、所定の形状・寸法精度・外観であることを確認する検査であり、検査項目・方法・許容差は「標仕」7.4.2の規定による。工場締め高力ボルトの締付け検査も含み、方法等は「標仕」7.4.7及び8の規定による。
(5) 溶接部の検査
溶接部の表l面欠陥・内部欠陥について、所定の許容範囲にあるかを確認する検査であり、検査項目・方法・許容差・合否判定は「標仕」7.6.10及び11の規定による。
(6) スタッド溶接部の検査
スタッド溶接部について、所定の形状・寸法精度・外観であることを確認する検査であり、検査項且・方法・許容差は「標仕」7.7.3及び5の規定による。
(7) 塗装部の検査
素地調整した面と塗装面について、所定の外観であることを確認する検査である。塗膜厚等の詳細な検査については、検査の有無、測定方法、測定時期、測定箇所等について特記に従う。
(b) 塗装部の検査以外の製品検査は、原則として溶接外観検査その他の検査指摘事項の修正等が可能な塗装前の時期に実施する。
途装の指定がある場合は、原則として塗装部の検査以外の検査を終了したのちに塗装する。
-
no image
-
no image
-
no image